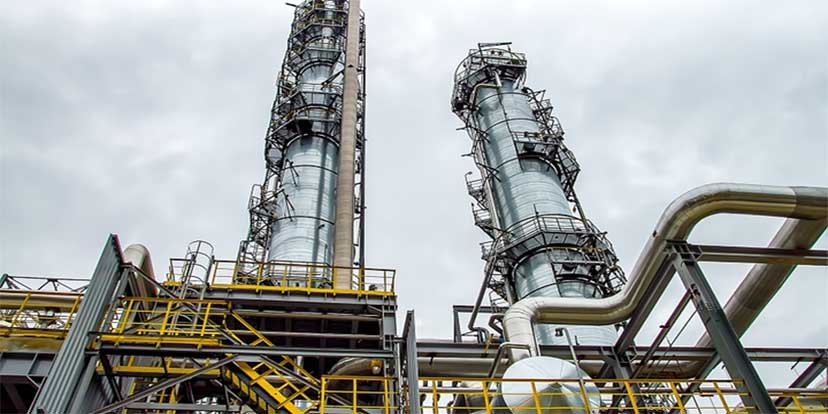
واحد آمونیاک
گاز طبیعی سبک با 95% متان ، به میزان 670 میلیون نرمال متر مکعب در سال (برای هر فاز)، از واحد بازیابی اتان دریافت و از ارسال میگردد و به دو صورت خوراک و سوخت مورد استفاده قرار میگیرد. با توجه به اینکه در فرایند تولید از آخرین تکنولوژی روز دنیا استفاده شده نسبت فلو مصرفی گاز سوخت به خوراک 25% می باشد در حالی که در تکنولوژی های قدیمی تر این نسبت تا 100% هم بوده است و لذا با انتخاب تکنولوژی جدید، کاهش مصرف سوخت هر فاز تا 160 میلیون متر مکعب در سال نسبت به تکنولوژی های قدیمی، صرفه جویی دارد. لذا این شرکت از همان اغاز رویکرد کاهش مصرف انرژی و به تبع ان کاهش قیمت تمام شده محصول را عملا اجرا نموده است.
گاز سوخت به عنوان منبع حرارتی در ریفرمر اول استفاده میشود و از آنجا که ترکیبات موجود در گاز طبیعی خوراک ، برای کاتالیستهای واحد مسمومیت ایجاد می نماید بایستی این ترکیبات مضر، از گاز جدا شوند. لذا گاز طبیعی ، در ابتدای ورود به واحد آمونیاک ، پیش گرم شده و ، دمای آن به 370 درجه سانتی گراد افزایش می یابد. سپس مقداری گاز هیدروژن به آن افزوده شده و به یک راکتور محتوی کاتالیست کبالت مولیبدن فرستاده می شود. در این برج ترکیبات گوگردی موجود در گاز طبیعی، با هیدروژن واکنش داده و گاز هیدروژن سولفوره تولید می نماید. برای جداسازی هیدروژن سولفوره ، در دمای 370 توسط دو برج محتوی کاتالیست اکسید روی ، این ترکیبات از گاز حذف می گردند
.
پس از حذف کامل ترکیبات گوگردی موجود در گاز طبیعی، بخار آب به آن افزوده شده و به یک کوره به نام ریفورمر اولیه فرستاده می شود. در این کوره ، مخلوط گاز و بخار آب، تا دمای 800 درجه سانتیگراد گرم شده تا در مجاورت کاتالیست نیکل، واکنش ریفورمینگ انجام و گاز سنتز، شامل منوکسید کربن و هیدروژن تولید شود.
جهت تکمیل واکنش ریفورمینگ متان به دمای بالاتر نیاز است، لذا مخلوط گازی موجود که شامل متان، منوکسید کربن و هیدروژن است، به یک راکتور دیگر ، به نام ریفورمر ثانویه که محتوی کاتالیست نیکل است، فرستاده می شود. ازت مورد نیاز برای تولید آمونیاک نیزکه از هوای محیط تامین و توسط کمپرسور فشرده شده است، به این برج تزریق می شود. در این راکتور، ضمن تکمیل واکنش ریفورمینگ متان در دمای 1200 درجه سانتیگراد ، اکسیژن موجود در هوا نیز مقداری از هیدروژن تولیدی را سوزانده و به آب تبدیل می کند
.
درخروجی این راکتور ، با استفاده از دو راکتور محتوی کاتالیست آهن و مس ، آب تولیدی واکنش، منوکسید کربن موجود در گاز سنتز را به دی اکسید کربن تبدیل می کند.
مخلوط گازی حاصله شامل هیدروژن، ازت و دی اکسید کربن می باشد. جهت جداسازی دی اکسید کربن از این مخلوط ، ازروش شستشوی گاز با حلال aMDEA در برج جذب استفاده می شود. aMDEA اشباع شده در برج جذب، در برج استریپر، احیا شده و مجددا مورد استفاده قرار میگیرد. گاز دی اکسید کربن جدا شده، به عنوان محصول فرعی، به واحد های تولید اوره ارسال می گردد.
به منظور حذف مقادیر کم منوکسید کربن و دی اکسید کربن موجود در مخلوط گازی و تبدیل مجدد آنها به متان، پس از گرم کردن گاز در یک مبدل حرارتی تا دمای300 درجه ، از یک برج واکنش محتوی کاتالیست نیکل استفاده میشود.
مخلوط گازی موجود که شامل هیدروژن و ازت می باشد، در ابتدا خنک شده و توسط یک کمپرسور دو مرحله ای تا 180 بار فشرده و پس از تبادل حرارت در مبدل های حرارتی و ابگیری توسط بستر های مولکولارسیو، به راکتور تولید آمونیاک به نام کانورتور که محتوی 4 بستر کاتالیست اکسید آهن است ، فرستاده می شود. در فشار 180 بار و دمای 450 درجه سانتی گراد، آمونیاک تولید شده و از کانورتور خارج میگردد. واکنش تولید آمونیاک ، تعادلی بوده و در یک مرحله 18 درصد آمونیاک تولید میگردد .لذا مخلوط گازی خروجی کانورتور با استفاده از یک سیستم تبرید، که شامل تعدادی مبدل حرارتی و یک دستگاه کمپرسور می باشد، تا 20- درجه سانتی گراد سرد می شود تا آمونیاک موجود در آن، مایع شده و از مخوط گازهای واکنش نداده جدا شودگازهای واکنش نداده، به کانورتور برگشت داده میشود و آمونیاک تولیدی ، ضمن کاهش دما تا دمای 33- سانتی گراد، به مخازن 20 هزار تنی ذخیره آمونیاک ارسال می گردد.
یکی از قسمت های جنبی واحد آمونیاک، بخش تولید بخار است. در فرایند تولید آمونیاک، مقدار زیادی حرارت ایجاد شده که صرف تولید 360 تن در ساعت بخار می گردد. بخار تولیدی به مصرف فرایندی در ریفورمر اولیه میرسد و همچنین به عنوان نیروی محرکه توربین های دستگاه های دوار خصوصا کمپرسورها استفاده می شود.
از دیگر بخش های جنبی واحد آمونیاک سازی، سیستم آب خنک کننده close loop می باشد . این آب به عنوان مایع خنک کننده در بخش های مختلف فرایند مورد استفاده قرار می گیرد و خود توسط لب دریا خنک می شود.